Vertical Pressure Vessels: Key to Efficiency and Environmental Protection
The vertical pressure vessel is a crucial apparatus for mass and heat transfer in vapor-liquid and liquid-liquid processes. Widely employed in industries like oil refining, petrochemicals, and pharmaceuticals, it facilitates material separation through key chemical engineering operations. The performance of this pressure vessel significantly influences production capacity, product quality, consumption quotas, and environmental considerations, impacting waste management and overall environmental protection for the entire plant and enterprise.
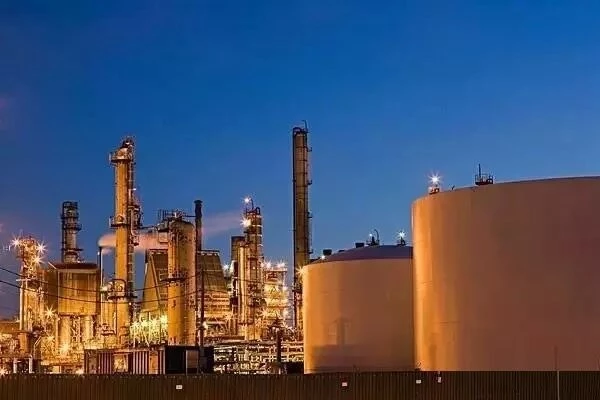
Vertical Pressure Vessels and Vertical Installed Equipment
Vertical pressure vessels and associated equipment are indispensable components within chemical plants, strategically placed to support diverse production processes. A vertical container, characterized by its round shape and vertical installation, encompasses various units like vertical vessels, reactors, and vertical tanks.
The vertical vessel stands as a pivotal piece of vertical equipment, holding significant importance in chemical and oil refining production. It facilitates efficient mass and heat transfer by establishing close contact between gas and liquid or liquid-liquid phases. Noteworthy characteristics include substantial size, a large aspect ratio, and considerable load-bearing capacity. Beyond pressure and temperature loads, the vertical vessel also withstands wind, seismic, and weight loads. Typically supported by a skirt support, the entire weight of the vessel rests on the skirt, secured to the foundation through anchor bolts.
Various Classifications of Vertical vessels
Key Components and Functions
Key components and functions of vertical vessels, whether plate or packed, include the tower body, support, manhole or hand hole, demister, adapter tube, hanging column, escalator, operating platform, and more.
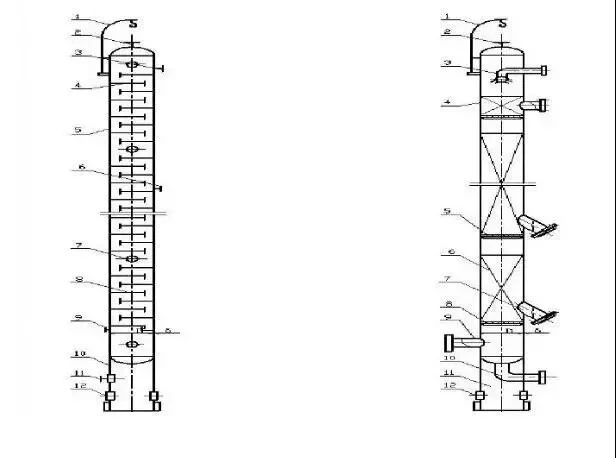
In summary, vertical pressure vessels are vital for mass and heat transfer in industries like oil refining and petrochemicals. Their performance influences production, quality, and environmental aspects, impacting waste management and overall plant sustainability. The diverse classifications and key components underscore their critical role in ensuring efficiency and environmental protection.
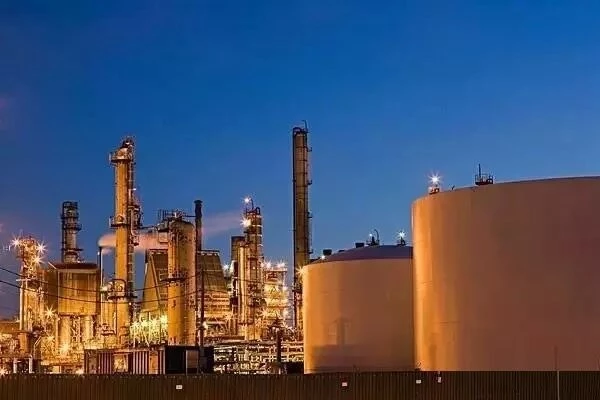
Vertical Pressure Vessels and Vertical Installed Equipment
Vertical pressure vessels and associated equipment are indispensable components within chemical plants, strategically placed to support diverse production processes. A vertical container, characterized by its round shape and vertical installation, encompasses various units like vertical vessels, reactors, and vertical tanks.
The vertical vessel stands as a pivotal piece of vertical equipment, holding significant importance in chemical and oil refining production. It facilitates efficient mass and heat transfer by establishing close contact between gas and liquid or liquid-liquid phases. Noteworthy characteristics include substantial size, a large aspect ratio, and considerable load-bearing capacity. Beyond pressure and temperature loads, the vertical vessel also withstands wind, seismic, and weight loads. Typically supported by a skirt support, the entire weight of the vessel rests on the skirt, secured to the foundation through anchor bolts.
Various Classifications of Vertical vessels
- Operating Pressure: pressurizing tower, atmospheric tower, and vacuum tower.
- Unit Operation: rectifying tower, absorption tower, desorption tower, quenching tower, reaction tower, drying tower, etc.
- Internal Structure: plate tower and packed tower.
Key Components and Functions
Key components and functions of vertical vessels, whether plate or packed, include the tower body, support, manhole or hand hole, demister, adapter tube, hanging column, escalator, operating platform, and more.
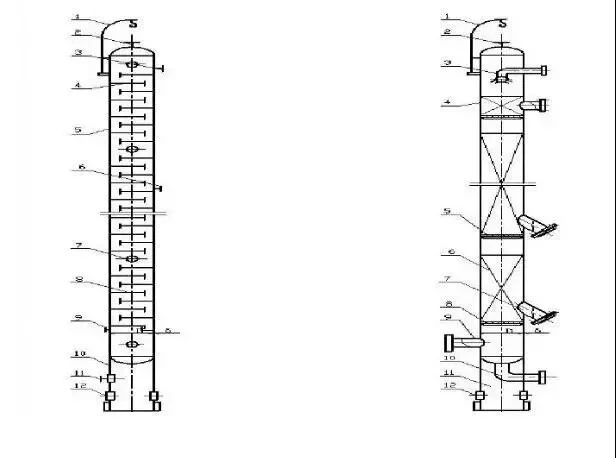
1. Tower Body: Serving as the shell of the tower equipment, the tower body comprises cylinders of equal diameter and thickness, along with upper and lower heads. Considerations extend beyond pressure and temperature, encompassing wind loads, seismic forces, and eccentric loads. The tower body must meet strength, stiffness, and stability requirements during pressure tests, transportation, and lifting.
2. Support: The tower support acts as the connection structure between the tower and the foundation, employing skirt-type support to ensure strength and rigidity due to the height and weight of the equipment.
3. Manholes and Hand Holes: Strategically placed for installation, maintenance, and inspection, these openings vary based on the specific tower equipment requirements.
4. Adapter Tube: Connecting process pipelines and other equipment, it serves various purposes such as liquid inlet and outlet, return, air inlet and outlet, side line extraction, sampling, instrument adapter, and liquidometer adapter.
5. Demister: Essential for trapping liquid droplets in airflow, influencing removal efficiency and separation effectiveness.
6. Hanging Column: Positioned atop the tower, it facilitates the lifting and transportation of internal tower components during installation and maintenance.
2. Support: The tower support acts as the connection structure between the tower and the foundation, employing skirt-type support to ensure strength and rigidity due to the height and weight of the equipment.
3. Manholes and Hand Holes: Strategically placed for installation, maintenance, and inspection, these openings vary based on the specific tower equipment requirements.
4. Adapter Tube: Connecting process pipelines and other equipment, it serves various purposes such as liquid inlet and outlet, return, air inlet and outlet, side line extraction, sampling, instrument adapter, and liquidometer adapter.
5. Demister: Essential for trapping liquid droplets in airflow, influencing removal efficiency and separation effectiveness.
6. Hanging Column: Positioned atop the tower, it facilitates the lifting and transportation of internal tower components during installation and maintenance.
In summary, vertical pressure vessels are vital for mass and heat transfer in industries like oil refining and petrochemicals. Their performance influences production, quality, and environmental aspects, impacting waste management and overall plant sustainability. The diverse classifications and key components underscore their critical role in ensuring efficiency and environmental protection.