Pressure Vessel Inspection: Safety and Reliability Guidelines
A pressure vessel serves as a sealed enclosure designed for the storage of gases or fluids. Operating at pressures significantly higher than the ambient pressure, these vessels pose potential dangers and can lead to fatal accidents. Therefore, it is imperative to conduct thorough inspections and safety tests on pressure vessels. Here are various aspects related to the inspection process:
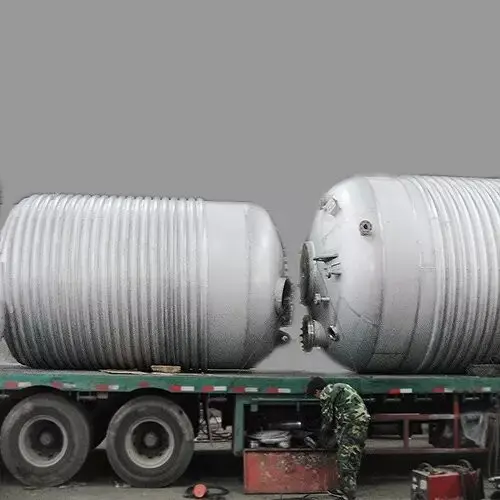
1. External Inspection (In-Service Inspection)
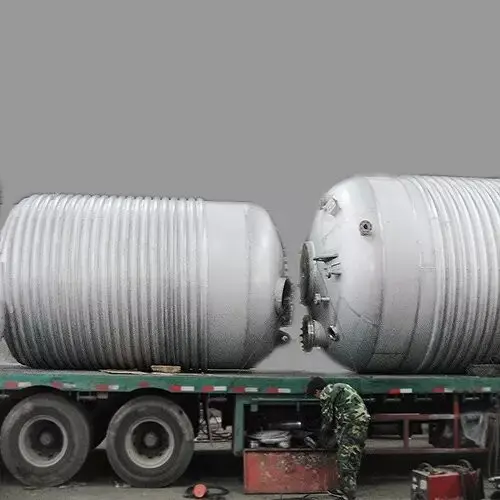
1. External Inspection (In-Service Inspection)
- The primary focus during external inspection, also known as in-service inspection, involves identifying abnormalities on the outer surface of the pressure vessel. This includes detecting issues such as cracks, deformation, leakage, and local overheating.
- Verification of the completeness, sensitivity, and reliability of safety accessories.
- Examination of the integrity and tightness of fastening bolts.
- Assessment of the foundation for abnormalities like sinking, tilting, and damage to the coating.
- External inspection is a shared responsibility between inspectors and daily operators. Any unsafe conditions should be promptly reported, leading to the shutdown of the valve system.
2. Internal and External Inspection After Parking
- This inspection is conducted after the pressure vessel has been parked, and the interior has been thoroughly cleaned.
- In addition to external inspection aspects, the examination includes checking for corrosion and wear on both inner and outer surfaces.
- Detailed scrutiny of welds, shell cover transition areas, and other stress concentration points for cracks using the naked eye and magnifier.
- Utilization of ultrasonic waves or radiographic inspection for internal weld quality assessment and wall thickness measurement.
- If wall thickness falls below the minimum required, a strength check, repair, or pressure-reducing measures are recommended.
- High and ultra-high pressure vessel bolts are subject to magnetic powder or coloring inspection for crack detection.
- Defect analysis and treatment opinions are submitted, and a retest is required after repair. The inspection cycle is typically every three years, with variations for corrosive or toxic media.
3. Overall Inspection
- In addition to the above inspections, an overall inspection involves a pressure-tight test, usually a hydrostatic test, and nondestructive spot testing of major welds or inspection of all weld joints.
- For low-pressure containers with non-flammable, non-toxic, non-corrosive media, nondestructive testing may be omitted based on experience.
- The overall inspection cycle is generally once every six years, with the possibility of extension for qualified containers filled with air and inert gas after confirming no corrosion through experience and internal/external inspections.