Guarding Against Corrosion: Strategies for Pressure Vessel Integrity (Part Two)
In the realm of pressure vessel maintenance, the quest for structural integrity requires a nuanced strategy for comprehensive corrosion prevention. Let's delve into detailed considerations and innovative methods aimed at ensuring prolonged service life and unwavering performance of the pressure vessels.
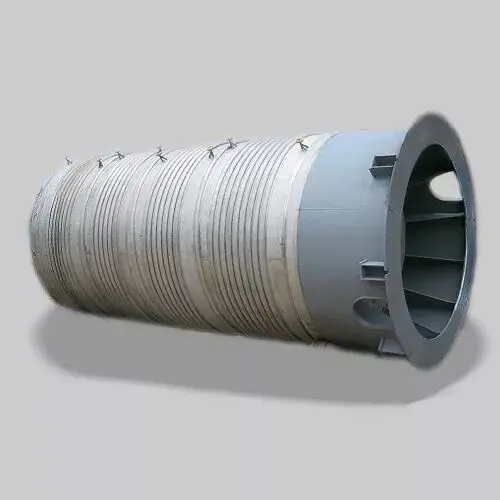
1. Selecting the Right Corrosion Inhibitor
2. Materials Tailored to Operational Conditions
3. Pioneering Research and Development of Materials
4. Harnessing Electrochemical Protections
By integrating these sophisticated strategies, operators of pressure vessels proactively mitigate corrosion risks, ensuring sustained performance, safety, and an extended operational life. These considerations underscore the importance of adopting a holistic approach to pressure vessel maintenance, emphasizing the dynamic interplay between corrosion prevention and diverse operational environments.
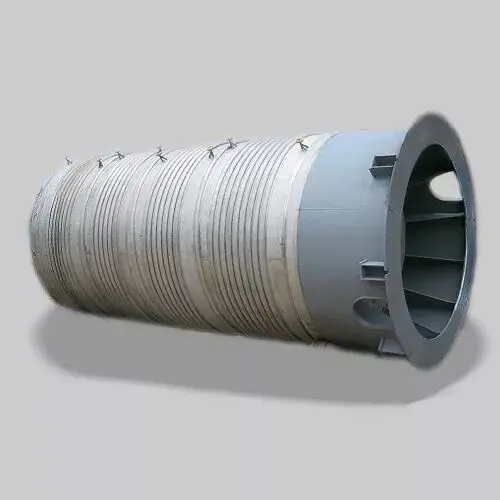
1. Selecting the Right Corrosion Inhibitor
- Precision in applying corrosion inhibitors to the metal surface significantly enhances corrosion resistance and reduces corrosion rates.
- Corrosion inhibitors, known for their cost-effectiveness in comparison to alternative anti-corrosion processes, demonstrate exceptional efficacy in managing chemical and electrochemical reaction corrosion.
- Explore classifications such as adsorption type (leveraging organic substances), oxide type (functioning as an oxidant and forming a protective film), and precipitation type.
2. Materials Tailored to Operational Conditions
- Material selection is a critical determinant, considering application conditions, adherence to standards, and resistance to high temperatures and pressures.
- Align material choices with solvent characteristics, steering clear of steel in highly reductive or humid environments.
- Adherence to relevant standards ensures construction quality and reduces corrosion risks, favoring materials with minimal intergranular gaps.
3. Pioneering Research and Development of Materials
- The evolving landscape of pressure vessel manufacturing introduces novel materials that elevate corrosion resistance.
- While metals and alloys remain prevalent, specialized components benefit from composite materials, especially for smaller structures.
- The ongoing pursuit of innovative materials addresses limitations in acid and alkali resistance, marking a crucial aspect of future-proofing against corrosion.
4. Harnessing Electrochemical Protections
- Electrochemical protection proves indispensable in thwarting corrosion reactions on the metal surface by transforming it into a cathode.
- Explore two primary methods: externally adding a DC power source to alter electron flow and utilizing sacrificial anodes with materials like zinc or aluminum.
- The continuous power supply or deployment of sacrificial anodes serves as effective measures adaptable to varying operational conditions.
By integrating these sophisticated strategies, operators of pressure vessels proactively mitigate corrosion risks, ensuring sustained performance, safety, and an extended operational life. These considerations underscore the importance of adopting a holistic approach to pressure vessel maintenance, emphasizing the dynamic interplay between corrosion prevention and diverse operational environments.